Our metal additive capabilities provide unparalleled design freedom, reduced lead times, and cost-effective solutions for complex and customized metal components in high-performance aerospace, defense, and medical industries. Castheon leverages cutting-edge metal printing technologies such as laser powder bed fusion to produce highly complex products that meet your exact specifications. Additionally, our team at ADDMAN Group can help you establish a tactical roadmap for developing additive manufacturing capabilities to gain a competitive advantage. Trust us to deliver the highest quality metal components and join us on the journey toward the future of additive manufacturing.
Metal Additive Manufacturing

Machines
Utilizing state-of-the-art technologies, we manufacture mission-critical parts that are lighter, stronger, and faster to market with additive manufacturing. As a leader in refractory metal additive manufacturing, the Castheon name is synonymous with high-quality, isotropic microstructures, advanced metallurgy, and print parameter development. We utilize over 15 industrial laser powder bed fusion (L-PBF) printers to continuously push the limits of printable geometries and customer applications. We develop custom material parameter sets to build rocket thruster assemblies, fuel nozzles/injectors, and high-performance thermal management assemblies for the aerospace and space industries. A number of cutting-edge machines are used by Castheon, including:
- EOS
- Velo3D
- Additive Industries
- 3D Systems
- GE Additive
- Nikon SLM Solution
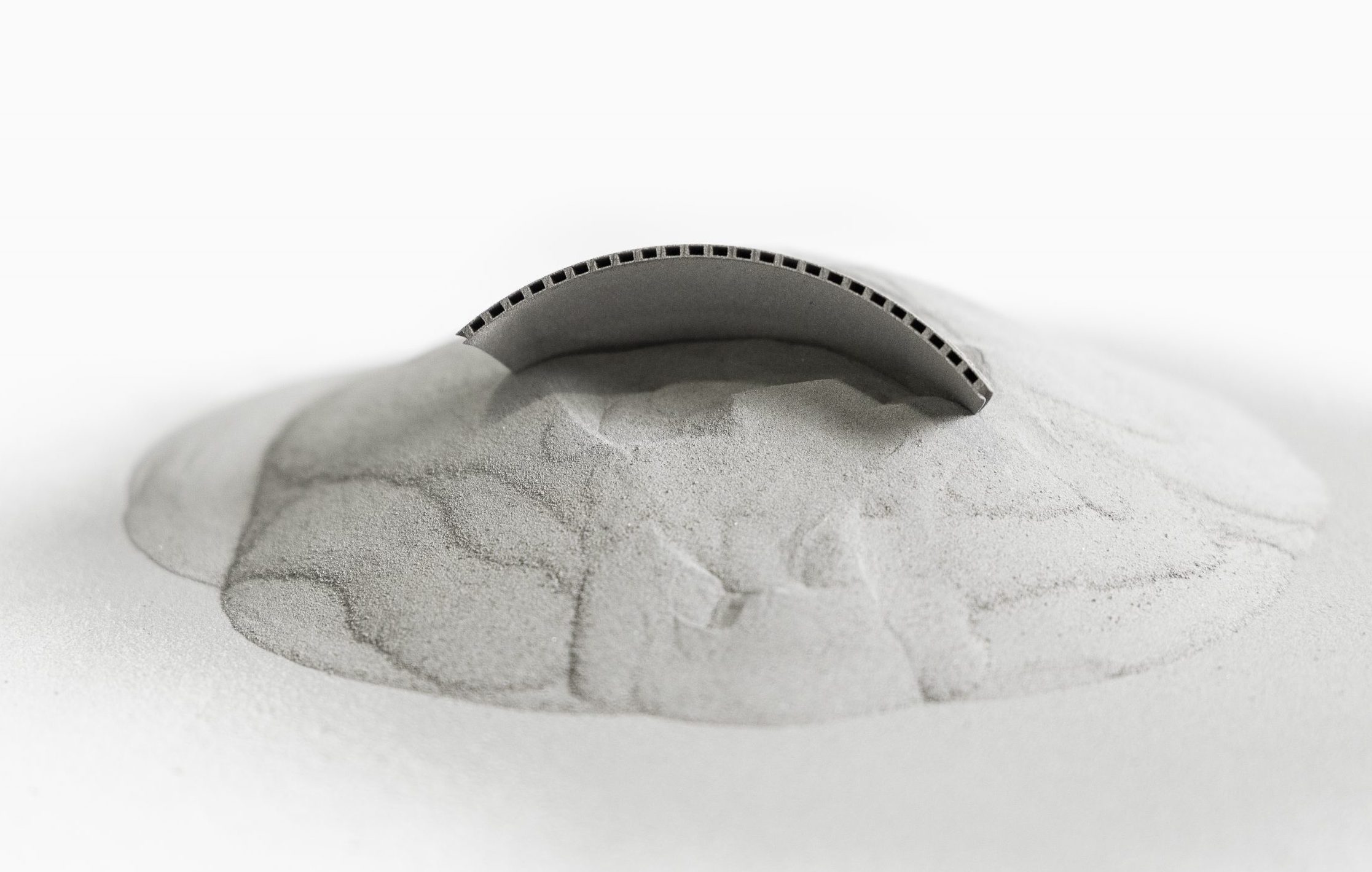
Materials
We offer a wide range of metal additive materials to meet the needs of various applications. Our extensive knowledge of material science allows us to optimize the properties of each metal for your specific application. We can create components with excellent mechanical properties, high-temperature resistance, and corrosion resistance, among other attributes.
- Refractory Nb C103, W
- Haynes 230/214/188/282/HX
- Inconel 718/625
- CuCr
- GRCop-84/42
- CPTi
- Ti6Al4V Gr 5, 23
- Al Alloys
Refractory Metal Expertise
Refractory metals, particularly niobium alloys, are gaining popularity in the aerospace industry due to their high strength, low weight, and excellent corrosion and wear resistance. However, these metals can be difficult to process and fabricate due to their high melting points and brittleness, limiting their use in some applications. Dr. Youping Gao and his team at Castheon have developed new ways to 3D print refractory metal components for hypersonic applications and the military and defense industry, providing precise control over material properties and microstructure while enabling the creation of complex geometries and designs. This breakthrough technology opens up new possibilities for the use of refractory metals in aerospace and defense applications, paving the way for the next generation of hypersonic missiles and defense systems.
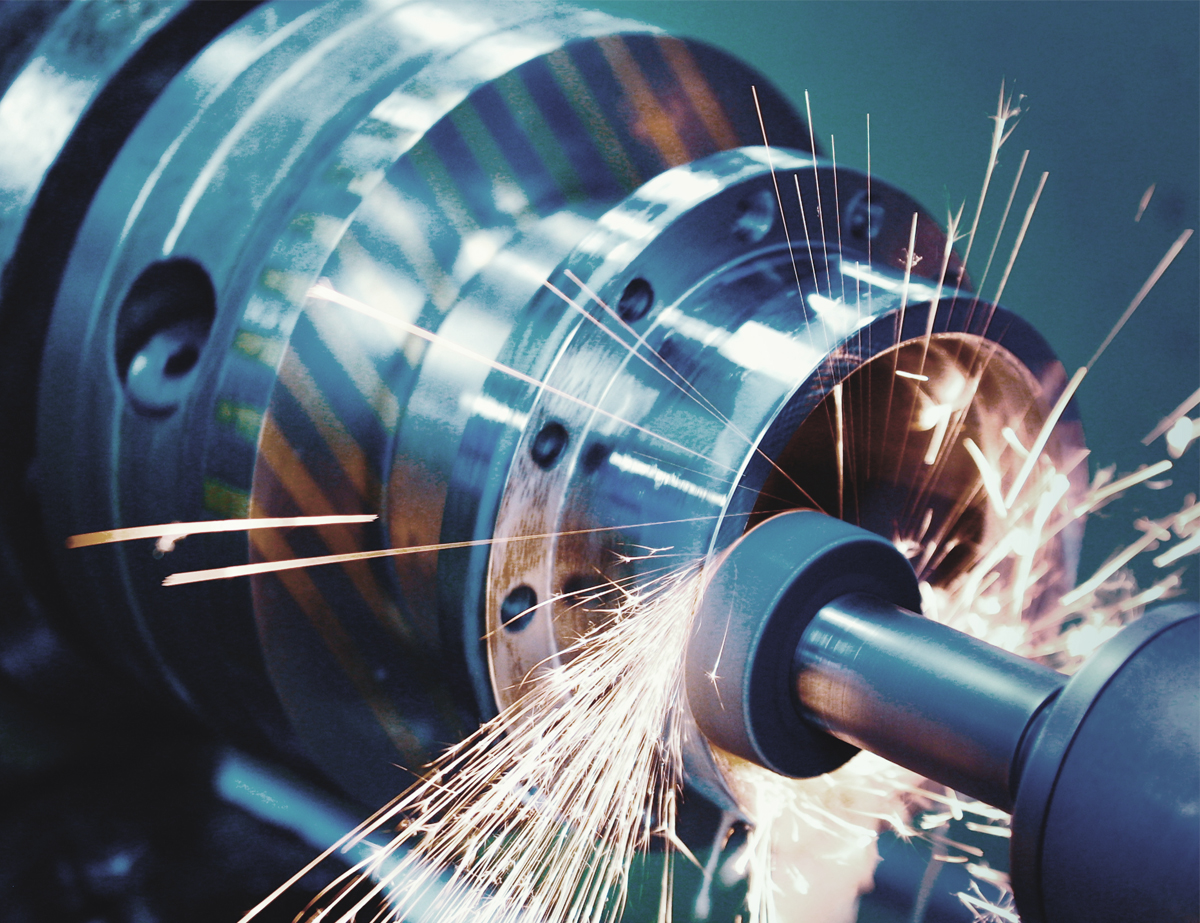
Post-Processing
HEAT TREATMENT
Mission critical quality often requires post-print processes like vacuum heat treatment, stress relief, and hot isostatic pressing (HIP) to reduce internal part stresses and optimize the properties of printed parts. After these processes, parts are typically removed from the build plate using wire electric discharge machining (wire EDM).
MACHINING
Many parts still require precision machining after heat treatment processes to meet tight tolerances. To provide a complete solution, ADDMAN offers over 100 traditional machines, including 5-axis CNC machines, turning stations, and wire EDM systems.
Together, we can speed up the innovation of tomorrow. Let's talk.
Our collective ability to create is boundless, limited only by the scope of our imagination. Your story is the starting point for this journey.